
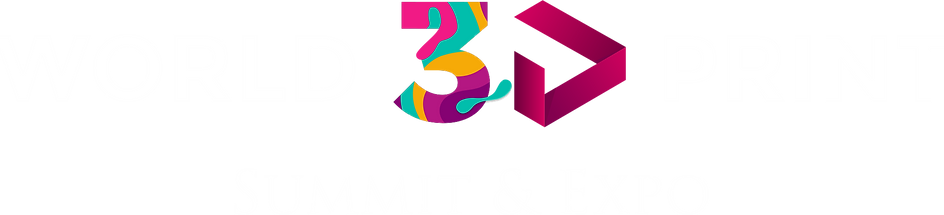
Aerosud is an established supplier of aero structure components and aircraft interior
systems with more than 25 years experience in product development and complex
industrialisation projects.
With the in-house availability of multiple manufacturing technologies together with
on time delivery and unquestionable quality, Aerosud is able to provide a competitive
total cost of business solution.
Our strive to be an ever flourishing company is driven through our investments in
research and development focused on complex metallic and thermoplastic forming,
additive manufacturing and advanced composite manufacturing techniques. In addition
our know-how in robotics and automation as well as collaboration in various
Industry 4.0 initiatives guarantees the continuation of our world class value offering.
​
“Your trusted partner for business and digital transformation.
The Fourth Industrial Revolution and digital transformation have become major strategic drivers to ensure future success.
Many organisations do not know how to start this transformation process or how to use it to their benefit or why digital transformation even applies to them. Furthermore, when an organisation decides to embrace this change they face the challenge of where to find the applicable know-how to make the right changes and to deal with the issues that will be faced.
Future technology is not as daunting as it may seem but it does require decisive planning and actions in order for businesses to withstand the threat of disruption and to thrive in an ever evolving environment.
Over the past thirty years Aerosud has gained real-life skills and experience across multiple business functions and systems in the innovative and competitive world of aerospace design and manufacturing and has become an internationally recognised supplier to the most significant aircraft manufacturer’s such as Boeing and Airbus. With this experience we have developed unique techniques to deal with business challenges and to find new opportunities. We are product agnostic and focus on satisfying our customers’ needs through the leveraging of existing and new technologies, best practices, and our unique skill sets as well as being able to identify the right resources via access to best-of-breed eco-systems.
We believe that we can share and transfer our skills and know-how to other business in such a way that it provides workable solutions that have a measurable effect on the growth and development of a business.
Our services and offerings we provide range from fit for purpose Product Life Cycle Management (PLM) systems, Enterprise Resource Planning (ERP) systems and Manufacturing Execution System (MES) solutions through to industrial and business process automation as well as lean and agile management methodologies. Included in our services and often overlooked are the softer skills that are crucial in order to ensure a successful transformation.
For more information on our services please contact us on octi@aerosud.co.za

Aditiv solutions is a manufacturer of high quality and affordable additive manufacturing equipment. With extensive experience in the development of AM systems, our focus is to provide cost effective metal 3D printing solutions.
Our HYRAX printer is designed to be the perfect tool for a wide range of applications where the manufacturing of complex geometries are required while minimising manufacturing costs.
HYRAX key features:
-
Build volume accommodates a wide range of geometries
-
Highest quality optical system to ensure consistency and accuracy
-
High build resolution allows for manufacturing of fine details
-
Allows for manufacturing of parts from a wide range of non-reactive metals
-
Small footprint makes it the perfect tool for any environment
-
Affordable price tag reduces production costs
Purpose of CAMASA
Establishment of a Growth-Bilateral between Government and Industry to significantly boost
South African Commercial Aerospace Manufactoring Exports through:
• Public-Private partnership
• Integrated Industry Growth Plan
• Expanding Advanced Manufacturing
• Future-orientated Competitiveness (IoT, Ind 4.0)
• Labour Engagement & Skills Development
Business Sector - Commercial Aerospace
• Commercial Aerospace - Aero-structures, Systems and Interiors
• Advanced Manufacturing (and Design & Engineering)
• Sector in South Africa - (CAMASA):
= 100 companies active
= Export R3.0b annually
= 40% Added Value (Local content)
= Employ 3 000+ people in high skill jobs
= Train 600+ people annually
= 90% of activity in Gauteng and Cape Town region.
CENTRE FOR RAPID PROTOTYPING AND MANUFACTURING (CRPM)
The early years
The CRPM is located at the Central University of Technology, Free State (CUT) in Bloemfontein and was established in 1997 as part of a research initiative. At that time, Additive Manufacturing (AM) also commonly know as 3D printing, was in its infancy worldwide.
What is 3D printing?
The official definition of Additive Manufacturing (or better known as 3D Printing), is “A process of joining materials to make parts or objects from 3D model data, usually layer upon layer, as opposed to subtractive manufacturing and formative manufacturing methodologies”. A design of the product is created which is translated into data and loaded on the 3D printing machine. The product can be “grown” using various powders, i.e. nylon, polystyrene, sand, titanium, maraging steel and many others. The powder is spread on a powder bed, a laser then sinters (melts) the first layer of powder, according to the data which has been programmed onto the machine from the design. This process is repeated over and over until the design has been manufactured into an actual product. The technology is advancing at such a rate that just about anything can be 3D-printed, from chocolate to human cells. It is versatile and offers solutions to manufacturing very complex designs that would not be possible to manufacture using conventional tooling.
​
The services we provide
As was mentioned earlier, the centre has offered a service to industry and produces parts for a wide range of clients, from automotive manufacturers to the aerospace industry, architects, jewellers, foundries and for many other interesting applications.
However, it was decided to focus on the medical niche and to use our pool of expertise to improve the lives of State patients where there is such a backlog of patients waiting for operations that they could be on the list for years. Patients with cancer or those who require radical surgery, might undergo surgery to remove the cancerous growths or repair the damage caused by traumatic incidents, leaving the patient with disfigurement, especially when parts of the face are removed. These patients not only are severely disfigured, but often are unable to eat, drink, and communicate normally. Unfortunately, there are no funds available at the public hospitals to assist these patients with prosthetics or reconstructive surgery and they are sent home to live their lives to the best of their ability, shunned by society and with a constant struggle to take in nourishment.
In 2012, the first South African 3D-printed implant was successfully implanted in Pretoria. This was a proud moment for all concerned. Since then implants have been produced and when the first mandible was implanted in the Kimberley Hospital in 2013, it received coverage throughout South African and in the global media.
​
The CRPM has assisted 30 patients, who under the present circumstances, would not have undergone any procedures to restore their dignity and quality of life. The interventions were done at no cost to the patient whatsoever, with the various role players donating their services as corporate social responsibility. However, there is a multitude of patients requiring assistance and the companies/institutions cannot continue to fund every case.
​
The CRPM team and expertise
The staff complement is very small but is highly skilled and includes experts who are involved in the activities of the centre on a part-time basis to provide specialised support, such as:
-
Dr. Cules van den Heever, Prosthodontist, as expert medical consultant on maxillofacial prosthetics
-
Mr André ten Napel who is the Medical Device Safety Officer and expert on ISO compliance
ISO certification
CRPM received ISO: 13485 (medical device) certification to manufacture custom implants, guides and models in titanium using AM. The centre can now design and supply medical devices globally as we meet the international standards set for these products. This is one of the first universities in the world to receive this certification.
Research Publications
As the centre is involved in both commercial and research work, a number of articles, papers and theses have been written and published in journals and other media. The staff has been invited to present keynote papers at many international conferences and their work has been cited in international research.
Akhani 3D is born out of our 15 years of experience in 3D Printing / Additive Manufacturing. We have capability and expertise in all the major technologies ranging from full colour binder jetting to direct metal. Our team has extensive experience in Design for Additive Manufacture and is skilled in providing solutions to take ideas from concept to reality.
​
Our current range of Additive Manufacturing technologies includes:
-
Stereolithography (SLA/DLP): The SLA process utilizes a vat of liquid photopolymer resin cured by ultraviolet laser to create solid 3D models.
-
Selective Laser Sintering (SLS): SLS employs a high power laser to fuse plastic powders into finished prototypes and functional end-use components.
-
Fused Filament Fabrication (FFF): Another additive manufacturing technology, FFF (similar to Fused deposition modeling (FDM)) uses a plastic filament, unwound from a coil to supply material to produce a part.
-
Composite (FFF): FFF parts printed with continuous fiber reinforcement using Carbon Fiber, Fiber Glass, Kevlar and high temp Fiber Glass
-
ColorJet Printing (CJP): Using an inkjet-like printing head to selectively deposit a colored liquid binding over a bed of powder material we are able to create full color finished parts. (Read More)
-
MultiJet Printing (MJP): An additive manufacturing process that prints thin layers of UV curable liquid plastics and wax support materials to create high resolution fully cured plastic parts.
-
Direct Metal Printing (DMP): Direct Metal Printing uses additive manufacturing technology. A high-precision laser is used on metal powder particles, producing horizontal metal layers.
With all these technologies at our fingertips and a continuous stream of projects – covering the straightforward, all the way through to imaginative, boundary-pushing designs – we’ve lived the 3D printing dream, warts and all.
For our clients, we can truly say, “We do this stuff”. And because we do this stuff day-in and day-out, we can call it like it is, complete with our trained-this-way engineering practicality.
Akhani 3D is not your usual ‘have a couple of 3D machines in the garage’ 3D print bureau service. Our approach is to enable our customers to transition their traditional manufacturing processes to an optimised Additive Manufacturing production process, wherever it makes sense.
The CSIR additive and advanced manufacturing centre serves to fast track the competitinvess of the South African manufacturing industry through its capabilities.
Engineered materials
-
Advanced, speciality materials with the potential to provide local downstream industry with competitive edge
-
Beneficiating local natural resources
-
Reduction of water, waste and energy
Part Fabrication
-
Integration of advancing of equipment and design optimisation to improve efficiency and reduce waste
-
Specialist part fabrication and equipment for local developed advanced materials
-
Advanced toolmaking
Manufacture of assemblies
-
Product technologies for advanced industrial equipment and machinery
-
Factory integration and optimisation technologies
-
Creative attractive environment for global OEMs in high end/advanced industries
SIMTEQ ENGINEERING specialize in providing the technology, training and knowledge transfer consulting services using Computer Aided Engineering (CAE) simulation solutions.
We make it simple to solve and prevent manufacturing and in-service problems of parts and assemblies using state of the art technology.
​
Our simulation solution eliminate costly and time-consuming trial-and-error prototyping, helping our clients to get products to market faster, cheaper and with confidence that it will perform its function as designed.
​
Our simulation solutions range from stress and structural analysis, fluid dynamics, multibody dynamics and manufacturing.
​
Manufacturing areas includes Additive Manufacturing (for both plastics and metals), welding and forming.
About
LambdaG is a technology company specialising in the design and manufacturing of advanced RF & microwave components. Our primary focus is the research and development of innovative antenna systems in the space, defence and aerospace domains.
​
Our origins
LambdaG was established in 2018 as a solution to the modern small satellite requirement for lightweight, compact and sometimes integrated antennas. This has led to its first co-funded contract to mature innovative microwave sub-assemblies and components utilising additive manufacturing. This technology is still in its infancy within the small satellite market and together with its strategic industry partner, NewSpace Systems, LambdaG seeks to offer the small satellite market lightweight microwave communication solutions with uncompromising electrical performance.
​
Our know-how is based on expertise in the development of a space-qualified GPS antenna, several defence related communication antennas and further research into phased arrays, pattern reconfigurable and integrated antennas. Our clients are busy innovating within their niche markets, this being small satellites, unmanned aerial systems and defence related. LambdaG is currently developing several requirement-driven RF & microwave products from L- to Ka-band as innovative solutions to the growing satellite communication needs.
Our offering
We offer standard or custom RF & microwave solutions up to 40 GHz. These products utilise technologies in microstrip, stripline and 3D printed waveguide. We specialise in antenna design, passive components and sub-assemblies which can be customised to your specific frequency, power and configuration requirements.
RAPDASA (Rapid Product Development Association of South Africa) is a non-profit organisation established in 1998 to create a community representing all facets of the Additive Manufacturing (AM) sector – from idea/concept, to design, prototype development into manufacturing and commercialization. RAPDASA is known as the official platform for rapid product development in South Africa, connecting leading innovators, entrepreneurs, industry partners and academics through various community engaging events. RAPDASA is recognised as the official mouthpiece of the AM in South Africa and strives to promote Additive Manufacturing as a vibrant technology in the 4th industrial revolution.
NewSpace Systems (NSS) is an advanced manufacturer of robust, space-proven
satellite sub-systems and components. A preferred supplier to the next-generation of
operational SmallSat constellations, the NSS team specialise in Guidance Navigation
and Control (GNC) solutions and manufacturing services (including technology
commercialisation and space-quality contract manufacturing). With its main stateof-
the-art manufacturing facilities situated in Cape Town, South Africa; NSS has a
subsidiary in the UK, 7 resellers globally and is currently exporting to 20 countries,
across 5 continents.
The NSS product range includes:
• GPS Receivers & Antennas • Fine Sun Sensors
• Magnetometers • Magnetorquer Rods
• Reaction Wheels • Closed-Loop GNC Solutions
• Stellar Gyros • Star Mappers
Committed to delivering high-quality products and services, NSS has established a
unique facility on the African continent comprising of several state-of-the-art ISO
14644-1 certified, class 10 000, cleanrooms, and technicians and assembly staff
who are European Space Agency accredited and follow the rigorous ECSS processes.
The accreditation of NSS, in the fourth quarter of 2017, with ISO 9001:2015 further
affirms the teams focus on quality.
Realize the value of the Digital Enterprise Suite. Additive Manufacturing is revolutionizing industrial manufacturing. Siemens is the only company in the world to offer integrated software and automation solutions for industrial use.
Use the digital twin to derive unique benefits from the Digital Enterprise Suite.
-
Reimagine products with the digital twin of the product
Additive Manufacturing gives you the freedom to create forms that would have been impossible using conventional manufacturing methods.
-
Reinvent manufacturing with the digital twin of the production and the performance
Additive Manufacturing optimizes the production process, setup, and configuration.
-
Rethink business
Additive Manufacturing enables flexible, fast, and efficient production. The process is perfect for custom production up to single-unit batches.
Siemens has powerful tools that allow you to execute the entire additive manufacturing process from design to print.
To learn more follow the link below:
https://new.siemens.com/global/en/markets/machinebuilding/additivemanufacturing.html
Follow the hashtag #AMoutOfAfrica on LinkedIn to learn more about the Siemens additive manufacturing portfolio.
The Stellenbosch Technology Centre - Laboratory for Advanced Manufacturing (STC-LAM) is part of the Industrial Engineering Department at the University of Stellenbosch. The centre is founded upon three main focus areas namely, Research and Development, Innovation Action Projects, and Education and Training. Our mission is simple: to deliver novel research, resource efficient solutions, and high quality education. State of the art equipment for both subtractive (3- and 5-axis CNC, wire- and die sinking EDM) and additive manufacturing (laser beam melting) is utilised towards maintaining the high quality outputs already established. This includes extensive technology transfer to industry with a large client base, as well as intensive national and international collaboration. We offer services regarding design, process chain development and prototyping, additive- and subtractive manufacturing solutions, and metrology for quality control and reverse engineering.
Research group 3D Innovation at Stellenbosch University does research and development of quality control, quality improvement and advanced biomimetic design, mainly focusing on X-ray tomography and biomimicry combined with metal laser powder bed fusion. All 3D technologies including scanning, image analysis and 3D printing are of interest.
For more on our research please see this site: http://blogs.sun.ac.za/duplessis.
We also offer CT scan services which can be found here: www.sun.ac.za/ctscanner
An electronic flyer will be available : http://blogs.sun.ac.za/duplessis
The VUT Southern Gauteng Science and Technology Park is a strategic technology hub in the Southern Gauteng region and is based at Sebokeng in the Vaal. It is supported by a multi-disciplinary skilled workforce, with 172 hectares of land and boasts world class technology programmes in Advanced Manufacturing, all geared to support industrialisation and job creation. To capitalise on our unique value proposition, we will make an impact in the region through focusing our capabilities in driving two flagship programmes, one in Advanced Manufacturing and the other in Agriculture Revitalization. The Advanced Manufacturing Precinct focuses on advanced product design and manufacturing for industries, particularly in the foundry and pioneering manufacturing sector. The facility functions as a service bureau, supporting local industry and entrepreneurs, as well as providing research support to local and international researchers. We offer a range of prototyping and manufacturing technologies, including binder jetting (BJ), fused deposition modelling (FDM) and laser sintering (LS). The facility has the ability to create useable prototypes and final components quickly and accurately, in a range of materials.